Having a controlled spray pattern for water is vital for several industries, including fire suppression systems, manufacturing, and even farming. If certain nozzles or valves crack, it limits the efficiency of the water flow and creates wastewater. Ordering replacement spray valves can help restore functionality to necessary systems. One area where a powerful stream of water has a big impact is that of fabrication.
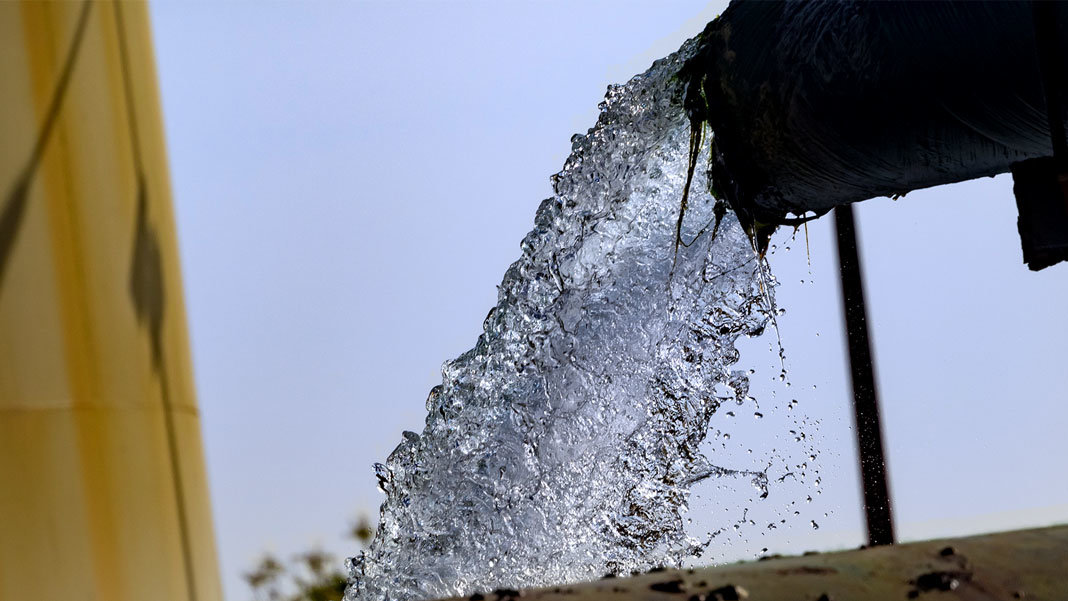
Enhancing Precision
A waterjet cutter is tool that relies on a jet of water released at high pressure and velocity to slice through metal or other materials. It can also rely on mix of abrasive substances and water to mimic the forces of nature that create water erosion. However, the use of a waterjet is more efficient. Because of the applications for manufacturing and fabrication, industries ranging from aerospace to mining rely on operations for reaming, shaping, cutting, or carving.
The Science Behind the Operation
The power behind the waterjet is a high-pressure water pump. Simply tapping into a water main won’t supply enough pressure for precision cutting. The water is ejected from a nozzle splitting whatever material is in its wake. Some of the additives that may be included for an additional abrasive effect can incorporate aluminum oxide and garnet. Because of the power associated with the spray, not every material should be cut with a waterjet. For instance, tempered glass will shatter when cut. One of the most significant positives of the waterjet cutting process is the ability for the material to cut without destroying the inherent structure of the material. Intense welding or heating can create weak pockets in the metal, which can damaging and change the intrinsic properties. A waterjet cutter keeps the structural integrity from being compromised.
Waterjet cutting is one way technology is creating a more efficient, less waste-producing manufacturing industry. The cuts are crisp, clean, and quick, giving companies more consistency with their products.